
Firing system characteristics
#16
Posted 13 June 2009 - 09:08 PM

#17
Posted 14 June 2009 - 01:25 PM
#18
Posted 14 June 2009 - 05:14 PM
I suspect it's an input circuit.
Ah yes, for status feedback, that would make sense!

#19
Posted 25 June 2009 - 08:32 PM
if you mave not met this chip in has built in basic and costs 2.50! one off.
I have come up with an even sexier circuit that physically locks both input and output and cost less than 1 pound.
Now does anyone know of a electronic componant that shorts on getting hot?
Green regard steve.
#20
Posted 25 June 2009 - 08:47 PM
#21
Posted 25 June 2009 - 09:18 PM
It was not clear what your circuit did. If the input at the left monitors the status of an channel output then why does it have a shorting switch across it? Why would you want not to monitor a channel? Also this kind of thing can't be scaled - you could not really have 64 switches (say) on a 64 channel unit.
The unit I have currently constructed (based on pic16F877) has 32 cues per box and boxes can be daisy-chained up to 1024 cues. All interlocks are software controlled apart from the 'top level' which is that the firing mosfets recieve no voltage until the key on the master unit is inserted.
Edited by phildunford, 25 June 2009 - 09:24 PM.

#22
Posted 04 July 2009 - 08:16 PM
My short pin is a phono which is also the arm plug. It locks the input till you arm the
unit. ( with the same plug ). It means you cannot loose the plug. Disabling the fire bar signal
is just a bonus and not really necessary.
I have knocked up the circuit see next post
Steve
#23
Posted 04 July 2009 - 08:45 PM

This is a rough sketch of the Q sequencer .
Notes :
The AXE 002 from Revolution Education. Tecsupplies CH1030.
Contains a PIXACE 18X and a ULA2008 octal darlington array.
One track cut is needed to take the ULA ground to the Arm plug.
The output Arm plug is the is same plug as the input safety plug, I use
a phono.
The continuity test is passive and does not involve the
microcontroller.
6 volt operation easily fires 3 matches per Q.
24 volt operation: remove R9 and wire in a 0.1 A 05 regulator.
Q 7 can be connected to other modules an so on.
I will buy a pint of cyder for any one to post me a nice drawing.
steve
#24
Posted 05 July 2009 - 01:29 PM
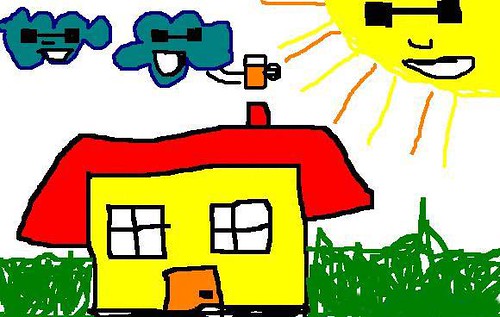
Nice enough?
#25
Posted 05 July 2009 - 03:38 PM
Nice enough?
Thats what my house looks like after a pint of cyder!
To answer an earlyer question; this thread started with an input that was active high so the input is best
shorted to gnd till ready to fire a 330R resistor would work as well. My circuit is active low so it is not so important.
I use a phono plug as the arm pin and a phono socket on the box is a good way to store it
Steve
#26
Posted 06 July 2009 - 04:07 PM
if the arm plug is in place on power up you could get an aciedental fireing.
Steve.
#27
Posted 01 October 2009 - 02:39 PM
another though was if i read correctly your using the output from an existing system to trigger this one and your not sure of the voltage ranges. if you have a comparator on the input it will only trigger if the input goes over a chosen voltage. this means you could either preset it of choose the input range. you could also set it to have an upper and lower limit.
if you intending on keeping costs down for any manufacture, relays are really expensive, same goes for any electro-mechanical device. you would be much better have a mos-fet output stage, maybe a H-bridge or something on those lines.
using a H-Bridge you could also be really cleaver and use a PWM controller to choose the current applied to the igniter, while keeping a constant voltage.
#28
Posted 01 October 2009 - 08:13 PM
using a H-Bridge you could also be really cleaver and use a PWM controller to choose the current applied to the igniter, while keeping a constant voltage.
Just a few points (there are more)
To be technically correct PWM does not control the current it controls the power as it is a series of on off pulses of differing mark space ratio (as I am sure you know).
It will also introduce unnessecary components (why reduce reliability) and possibly noise which will have to be suppressed (depending on isolation technique). There are plenty of cheep current limiting FET's with overload protection so why not use one (as you will probably need a FET anyway as an output stage)?
H-Bridge? Why would you want different sources to change the current to the ignitor? Just design for more than enough current for intended purpose.
#29
Posted 01 October 2009 - 08:55 PM
Just a few points (there are more)
To be technically correct PWM does not control the current it controls the power as it is a series of on off pulses of differing mark space ratio (as I am sure you know).
It will also introduce unnessecary components (why reduce reliability) and possibly noise which will have to be suppressed (depending on isolation technique). There are plenty of cheep current limiting FET's with overload protection so why not use one (as you will probably need a FET anyway as an output stage)?
H-Bridge? Why would you want different sources to change the current to the ignitor? Just design for more than enough current for intended purpose.
PWM varies the power by keeping a constant voltage amplitude and the pulse width of the signal varies the current and there for the power. idea being if the pulse width is 50:50 then the available current is 1/2 with a constant voltage amplitude. well at least the was my understanding.
the reason i suggested variable current was because there was a mention of battery power. therefore reducing any waste would mean either smaller battery or longer battery life. being being desirable.
PWM and H-bridges now come in single IC's with very little amounts of passive components required. complexity wise not alot different and would still be cheaper than a relay. plus in comparison to relays that will fire high current and switch off and on for 20 ms firing these wouldn't be cheap.
#30
Posted 01 October 2009 - 09:23 PM
Into a resistive load which is what we have here, the simple V=IR holds true so when the voltage is present the current is constant. I am afraid you are thinking of what you will see on a current meter that does not react as fast as the circuit as it is designed to measure the RMS value otherwise you would have a very blurry display switching between 0 and measured value.
So in conclusion the RMS value changes however the instantaneous value does not. As the blow time for a commercial ematch is pretty dam quick (if I knew the time I would say) there is a good chance the match will blow on the first rise.
The amount of power required to fire an ematch is minuscule compared the power drain for leaving the firing system on/armed. The best power saving strategy is to minimise component count along with component selection and removing all unnecessary loads.
It may be cheaper than a relay but not a fancy FET for no real benefit.
By the way I am not having a go. I think well reasoned debate is useful so that others can use the information to in any way they wish to make a well informed choice.
D
Edited by digger, 01 October 2009 - 09:39 PM.
1 user(s) are reading this topic
0 members, 1 guests, 0 anonymous users