
D-I-Y WASP Shell Pasting Machine?
#121
Posted 13 November 2012 - 11:38 PM
#122
Posted 13 November 2012 - 11:41 PM
#123
Posted 15 November 2012 - 02:27 PM
so Hopefully I should be able to start making one this weekend/next week

#124
Posted 19 November 2012 - 02:46 PM
He cut me some motor plates for the NEMA 34 motors, so once I have the plates back form my mate I can weld them all together.
I also made I shaft for the drive wheels out of aluminum round bar, I've just to drill it for the motor shaft and the grub screws.
I have the power supply and the stepper bee + and the software is being worked on, so all I need to do is make the top arm and bearing brackets then I should be ready to try it

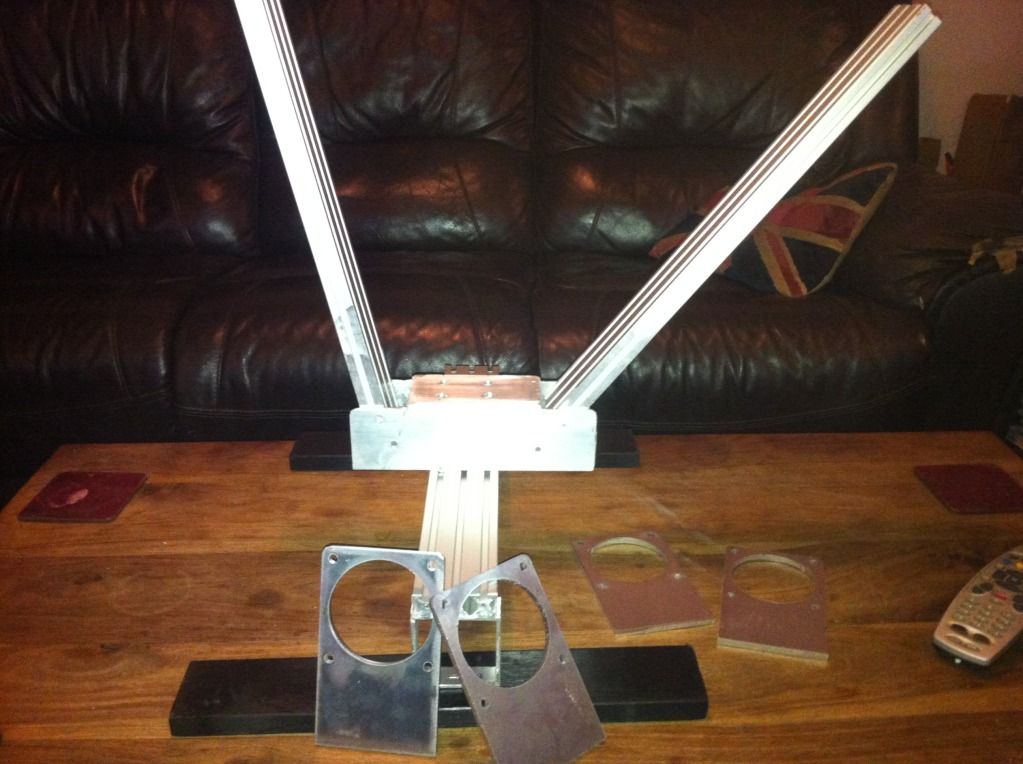
#125
Posted 19 November 2012 - 09:52 PM
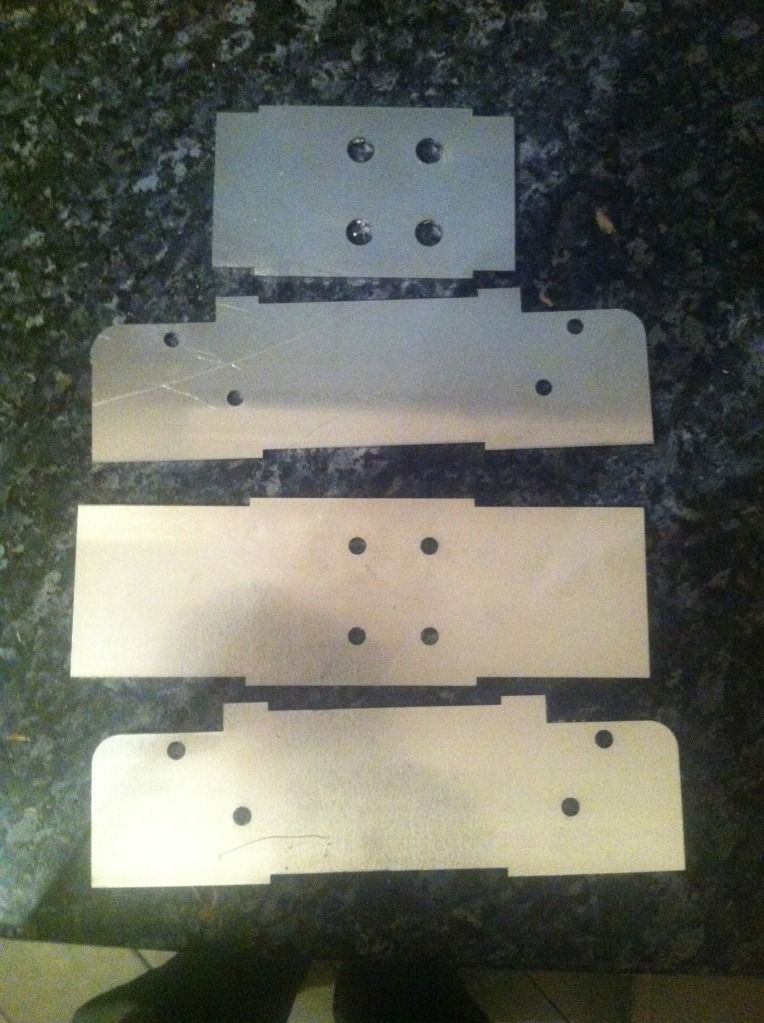
#126
Posted 20 November 2012 - 01:29 AM
The spine will be fine, the Mini just uses two plates on the sides and that's it.
#127
Posted 20 November 2012 - 03:06 PM

#128
Posted 20 November 2012 - 09:25 PM
If you use a narrow drive roller like the finned rollers illustrated, you will have to make the motor positions adjustable for different shell sizes. Of course this is possible, but it makes the mechanical construction more complicated, and when you move the motors you have to be careful that the positions are exactly symmetical. Using wider rollers means this uncertainty is taken care of once and for all when you build it. You don't particularly need a soft surface, just one that doesn't slip.
Just because it says in a stepper motor spec that it runs at 4V, or whatever, doesn't mean you can run them at 4V or dispense with the series resistors. They would work, but would have no torque at higher speeds. The reason for this is that driving stepper motors involves switching current on and off into inductive loads, and inductors have a time constant. That's to say, the current doesn't rise immediately to its limiting value, but rises exponentially with a time constant of L/R (inductance over resistance). Torque is proportional to current. So when you want it to turn fast and the steps are short, you have to adjust that L/R time constant so that the current rises to an adequate amount within the short time allowed, otherwise you have no torque. Since you can't reduce the L, you can only do it by having a larger R. That's why you typically see a motor rated for 4V, driven from 24V with huge smoking hot resistors in series. These days there are specialist stepper driver chips available that drive the motor with constant current - constant current equals infinite series resistance, within the working range - and since they behave like switching regulators they don't get hot.
More info here: http://www.allegromi...or-Drivers.aspx
#129
Posted 20 November 2012 - 10:45 PM
the stepper bee + uses Intelligent MOSFETs so i think it should be upto the job plus the motors I have run off a 3.78v power supply so I went with a 5v 20A power supply and i might get away without any limit resistors especially if the
motor does not spend too much time stationary.
#130
Posted 22 November 2012 - 01:23 AM
The round bar is for the motor shaft and drive wheel and the square block is for the top arm hinge.
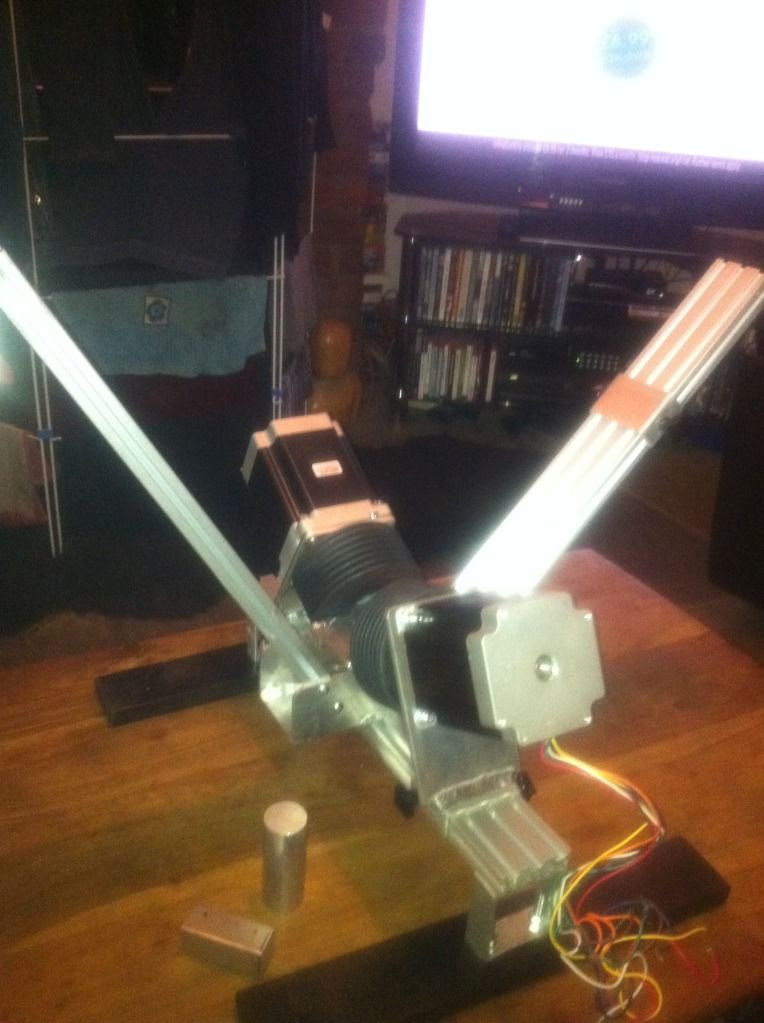
#131
Posted 22 November 2012 - 07:10 AM

The Fixtureworks drive rollers are 1.98" wide, the fabricated ones you suggested were 2" wide so I'm thinking they are an appropriate sub. They do make 2" diameter by 1.98 wide rollers which I really did consider using but since I'm using 570 oz/in motors I figured the 4" would be ok. If not I'll step down to the 2" or have some made. I'm really trying to avoid having anything made though, trying to make it an off the shelf or fabbed with common tools kinda project.
#132
Posted 22 November 2012 - 09:09 PM
i was wondering when we can book some pasting time, barnsley isnt too far.
Paul.
2KNO3(s) + 3C(s) + S(s) -----> N2(g) + 3CO2(g) + K2S(s)
#133
Posted 22 November 2012 - 09:19 PM
#134
Posted 23 November 2012 - 06:35 PM
#135
Posted 24 November 2012 - 01:09 AM
1 user(s) are reading this topic
0 members, 1 guests, 0 anonymous users